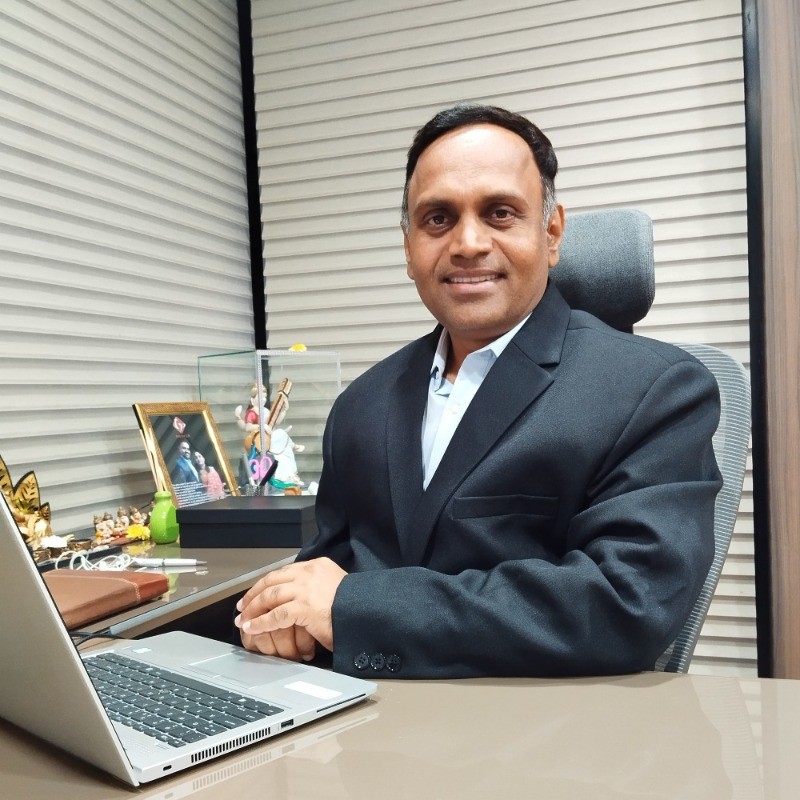
Sambhaji Bhikoba Chawale
Chief Executive Officer
PRIMATHON 2.0 is an exciting hackathon organized by PRIMUS Techsystems to foster innovation and creativity among participants. This event provides a platform for developers, designers, and entrepreneurs to collaborate and build innovative solutions to real-world problems. With various challenges and opportunities for learning, PRIMATHON 2.0 aims to bring together the brightest minds to create impactful projects.
Before registering for PRIMATHON 2.0, we kindly request that you begin by familiarizing yourself with the guidelines. Your understanding of these guidelines will ensure a smooth and compliant registration process for this exciting event. CLICK HERE FOR THE GUIDELINES.
For Idea Submission, use only specified format CLICK HERE FOR PRESENTATION FORMAT.
Complete your registration for PRIMATHON 2.0 by clicking the registration link below. Once you're on the registration page, kindly provide all the necessary details correctly, including information about yourself and your team members, in the provided form. Your participation in this event is just a click away!
RegisterPRIMATHON is a crucial event for PRIMUS Techsystems as it brings together innovative minds to solve industry challenges. By participating, we harness creativity and technical expertise, which fuels our company’s growth. This event helps us discover new solutions, expand our network, and foster a culture of collaboration. It also gives us the opportunity to stay ahead of the competition by leveraging the latest technological advancements that come from diverse perspectives.
Themes
No problem is too big... No idea is too small.
Intelligent IoT-driven Products for Data Insights
Discover innovative data products that leverage IoT technology to provide intelligent insights. The solutions enable real-time data analysis, empowering businesses to make informed decisions, enhance operational efficiency, and drive growth.
Robotic Process Automation
Using Robotic Process Automation (RPA), develop innovative solutions that automate routine tasks, enhancing efficiency and enabling smarter decision-making within your projects.
Development and Deployment
Empowering Innovation with Low-Code/No-Code Development in Cloud and DevOps.
Artificial Intelligence & Machine Learning
Explore the transformative power of Artificial Intelligence (AI) and Machine Learning (ML) to develop innovative solutions that drive automation, enhance decision-making, and unlock valuable insights from data.
Intelligent Enterprises
Enterprises leverage advanced technologies and data-driven insights to enhance decision-making, streamline operations, and foster innovation.
Simplified Integration
Leverage the CPI/BTP integration tool and PIPO to create streamlined wrappers that facilitate the development of new products, enhancing connectivity and accelerating integration across systems, enabling faster innovation.
Tentative hackathon schedule
14th October
Read guidelines of PRIMATHON 2.0. Choose one problem statement and create a unique presentation showcasing your vision, strategy to build a solution.
14th October
Discover the challenge that will drive innovation at PRIMATHON 2.0 with our official problem statement reveal!.
14th October
Participants will start to submit the idea they’ve finalized and will be working on for the rest of the hackathon.
25th October
ASK ME ANYTHING session and Problem Statement Explainer Session through which participants get chance to interact and solve their problems .
24th November
The window for idea submissions for PRIMATHON 2.0 is closed.
08th December
Announcement of the shortlisted teams for PRIMATHON 2.0 finale.
8th - 21st December
Mentoring and Training Sessions Of shortlisted teams to refine their idea for grand finale by industy experts.
23rd December
The finalist teams showcase their projects and innovations to the judges for evaluation.
December
Top teams are revealed and celebrated for their outstanding achievements.
At PRIMATHON 2.0, we believe in recognizing and rewarding exceptional talent and innovation.
₹ 60,000/-
₹ 30,000/-
₹ 15,000/-
Chief Executive Officer
Chief Business Officer
Chief Technology Officer
Chief Competency Officer
Chief Business Officer
Chief Business Officer